Plastic injection molding is one of the most convenient methods to fabricate finished plastic material parts. This process requires an injection machine, raw plastic material and a mold (usually machined from aluminum or steel) that holds the melted plastic until it cools and solidifies into the final product.
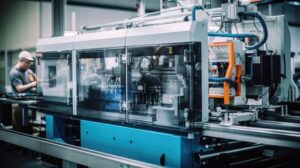
Once a design is ready, professional machinists make the tooling mold. The quality of this mold has a significant impact on the finish and dimensional tolerances of your parts. Read on Plastic Injection Mold Service Florida for more information.
The choice of materials used in injection molding can have a significant impact on cost, performance and aesthetics. The best injection molding company will have the knowledge and experience to help determine the correct material for your product. Different materials offer unique properties that can improve the overall quality and reliability of your final product.
Plastic resin comes in small pellets and is heated to a liquid state before being injected into the mold cavity. This process is a fast and economical way to produce large volumes of molded products. The type of plastic selected will directly affect the finish and dimensional tolerances of the finished parts.
Polyethylene, or PE, is one of the most common injection molding materials and offers a great balance of flexibility, durability, and cost. This versatile plastic is found in everything from milk jugs to car batteries. It can withstand high temperatures and is easily recycled. Polypropylene, or PP, is another popular plastic for injection molding that has high strength and elasticity and resists moisture and bacterial growth. It is easy to work with and can be molded into live hinges.
Acrylonitrile butadiene styrene, or PMMA, is also a popular injection molding material. It has a high transparency and gloss with good abrasion resistance. It can withstand a variety of chemicals, including some acids and bases. It is a good choice for cases for computers and laptops.
Adding threaded metal inserts can increase the strength and structural integrity of injection molded products. This can add stability and allow for screw or bolt connections. The insertion of these threaded components is usually done during the injection molding process, and can be completed with precision.
Another option for injection molding is to use a vacuum forming technique, which can be used to create hollow parts. This method can also be used to create curved or angled surfaces. This is often referred to as a “two-shot” injection molding process and provides greater versatility for the finished product.
Injection molding is a great option for producing prototypes and end-use production parts because of its low operating costs and high-quality products. The injection molding process uses automated equipment and robotics to reduce labor costs, resulting in lower production costs for each part. Injection molding can also save you money on assembly and finishing because the products are typically produced in the finished state, eliminating the need for additional steps like painting or machining.
Design
A quality plastic injection molding manufacturer is able to produce products with tight tolerances. This is made possible by using high-quality materials, sophisticated design software and rigorous inspection quality programs. The engineering phase involves developing a detailed injection mold from a sample part or drawing. The complex designs format the tooling that shapes the injection mold for the product. The injection mold must be able to hold composure under the injection pressure process for thousands of cycles without degrading or leaking.
The most significant cost driver in injection molding is the cost of the tooling. Injection molding tooling costs are fixed, irrespective of the number of parts manufactured. Hence, any changes to the mold design should be done with an eye on reducing the overall cost of the injection molded part.
Injection molding services include the injection of molten plastic into a mold cavity and the cooling of the molded product to maintain its shape. Injection molding can be used for the production of a wide range of consumer and industrial products.
During the design process, Abtec engineers will look at the dimensional criteria for the finished product and will ensure that the mold will meet these specifications. They will also consider factors such as cavitation, mold construction and tie bar distance during the overview process.
A key consideration is the location of the parting line, which is where two halves of the mold come together. A well-positioned parting line can help reduce secondary machining and improve the integrity of the resulting injected product. Abtec engineers will look at the parting line in terms of both the line of draw and the positioning of the core and inserts.
Another factor is the length of time the molded product takes to cool down and solidify to its final form. This cooling stage is a critical component of the molded product and should be taken into account during the design stage. Injection molded parts with undercuts may require a shut-off to eliminate the undercut.
Other design features to be considered for an injection molded product include the inclusion of fasteners, such as screws or bolts. These can be added to the product by designing a thread directly on the surface of the plastic, by using a side action core or by including a threaded insert. It’s important to note that when adding fasteners to a plastic injection molded product, the tolerance must be limited to +/- 0.250 mm (0.010″).
Tooling
Injection molding is a high-tech process that involves a sophisticated machine called an injection mold. The injection mold shapes the plastic into the final product using intense, controlled pressure. To maintain precision and accuracy, this machine requires sophisticated tools. Modern tooling includes computer-aided design (CAD) and manufacturing software, advanced materials, and innovative techniques. These technologies allow manufacturers to produce highly complex products with tight tolerances and superior surface quality.
The injection molding machine and its tooling are the heart of the entire plastic injection molding process. The equipment must be of the highest quality and capable of enduring rigorous use over thousands of injections. That’s why we use a comprehensive inspection process to ensure the safety and reliability of all our machines.
To guarantee the quality of your injection molded products, our engineers take your specific production needs into account from the outset of the project. We also understand the restrictions and possibilities of the injection molding process, so we can design your parts with a clear understanding of your production goals. This helps us deliver a high-quality product with a competitive cost.
The choice of materials for the mold and the injected plastic is another critical aspect in the success of an injection molding project. Different thermoplastics have varying flow and shrink rates, which must be taken into account during the design phase to avoid issues like warping or sticking. To ensure the durability and longevity of your plastic injection molds, we utilize high-quality steels and other materials that can withstand harsh conditions and repeated use.
Depending on your project’s volume requirements, we can optimize the number of cavities in your plastic injection mold to reduce upfront costs and speed up production time. We can also use angular slides and lifters to create recessed features in your plastic injection molds, increasing the versatility of your finished product. We have years of experience in molding complex, heavily filled Engineered Thermoplastics and can assist with material selection during the part design phase.
If you need to transfer your injection molds from one injection molding service provider to another, we offer swift and responsive tool transfer services. Our team is ready to handle the evaluation and documentation required for a successful move, so you can be confident that your plastic injection molding tools will be in good condition when they arrive at the new facility.
Production
Injection molding is an automated procedure that reduces human error and saves on supervision costs. The process is also streamlined with the help of self-gating technology, which simplifies operations and manufacturing while decreasing the chance for human error. The resulting plastic parts are very affordable to produce, especially with the high volume that can be produced at one time using this method.
Depending on the size and complexity of a part, production can be as quick as 24 hours from start to finish. Once a prototype is approved by the customer, it can be sent into the injection mold machine to create thousands or millions of optimally processed and finished plastic material parts. Once the tooling and prototype is finished, a series of tests are performed to ensure the molded product meets all specifications. This is when the final product really begins to come to life.
In the electronics industry, injection molded parts are used to make circuit boards, switches and support for completed systems. They can be made from conductive or non-conductive plastics, paired with waterproof seals and UV resistant coatings to meet specific product requirements for both durability and aesthetics. This is where the versatility of plastic really shines, as it can be molded into many different shapes and sizes without losing any structural integrity.
With plastic injection molding, there are many options to choose from for surface finishes as well. Some plastics have natural smooth surfaces, while others may need a special treatment to enhance appearance and provide traction for a particular application. Oftentimes, color is a consideration as well. Plastic is extremely versatile in this regard as it can be molded into various compounds and colors, including clear to cyan and everything in between.
Injection molding is a highly repeatable and consistent process, which is important for industries like automotive and medical devices where minor deviations can have severe consequences. Injection molding can achieve tolerances of +/-.0005 inches, which is far tighter than the tolerances possible with CNC machining. Injection molding is also a very efficient and environmentally responsible process. Unlike other manufacturing processes, plastic injection molding does not require heating or melting of raw materials. This allows for the use of recycled and reprocessed materials, helping to minimize environmental impact.